Water resistance test at Hublot
That is brief info from the net, how the HBB water resistance test is performed by Hublot:
The first step is to test the watch cases (without the movements) water-resistance. This is done by placing the empty cases on trays, which are then inserted into the “wet pressure†testing machine. This type of equipment reproduces the underwater pressures of different depth ratings; typically between 5 and 10 bars. (For the Oceanographic 4000, Hublot had to invest in a new type of water-resistance testing machine that could emulate the crushing pressures at 4000 meters below sea level).
Once the first water-resistance test is completed, the trays are removed from the pressure machine and the cases are air-dried. Then, the cases are placed on a metal “hot-trayâ€, usually pre-heated to 55?C.
This is to test for thermal shock, as after sitting on the hot-tray for a few moments, the cases are then placed, crystal side down, on a cold-tray (between 15?C and 17?C) for about 20 seconds. Then, if any condensation was to appear under the crystal, then the watches would fail the thermal shock and water-resistance tests; resulting in the disassembly of the case and inspection of individual components.
The majority of cases, however, do pass this first round of tests, and are then sent back to the watchmakers to have their movements fitted it. After that, the same set of tests is repeated, this time with functioning cases.
The measuring devices, used for testing, are produced by ROXER S.A., Swiss
That is brief info from the net, how the HBB water resistance test is performed by Hublot:
The first step is to test the watch cases (without the movements) water-resistance. This is done by placing the empty cases on trays, which are then inserted into the “wet pressure†testing machine. This type of equipment reproduces the underwater pressures of different depth ratings; typically between 5 and 10 bars. (For the Oceanographic 4000, Hublot had to invest in a new type of water-resistance testing machine that could emulate the crushing pressures at 4000 meters below sea level).
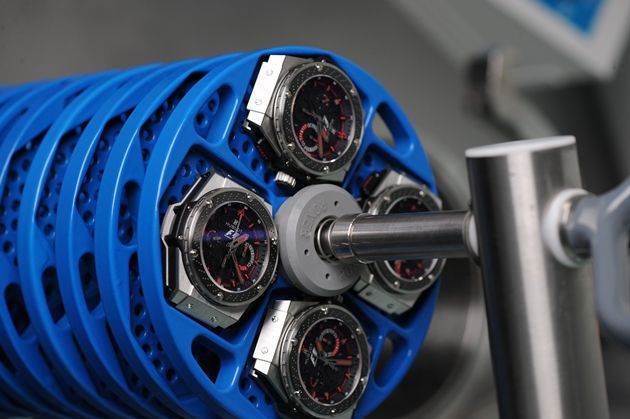
Once the first water-resistance test is completed, the trays are removed from the pressure machine and the cases are air-dried. Then, the cases are placed on a metal “hot-trayâ€, usually pre-heated to 55?C.
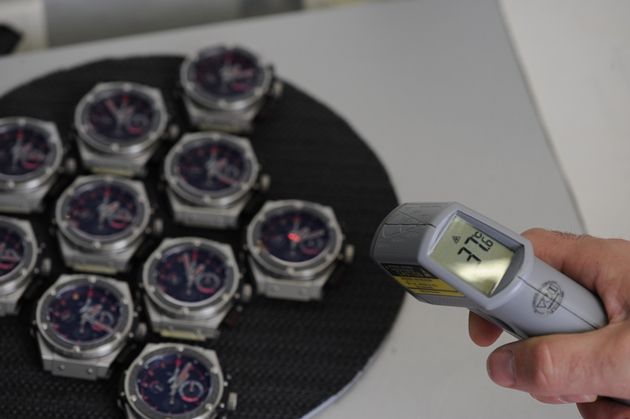
This is to test for thermal shock, as after sitting on the hot-tray for a few moments, the cases are then placed, crystal side down, on a cold-tray (between 15?C and 17?C) for about 20 seconds. Then, if any condensation was to appear under the crystal, then the watches would fail the thermal shock and water-resistance tests; resulting in the disassembly of the case and inspection of individual components.
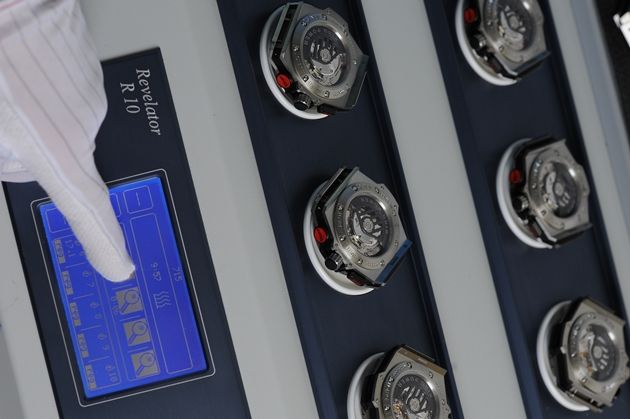
The majority of cases, however, do pass this first round of tests, and are then sent back to the watchmakers to have their movements fitted it. After that, the same set of tests is repeated, this time with functioning cases.
The measuring devices, used for testing, are produced by ROXER S.A., Swiss